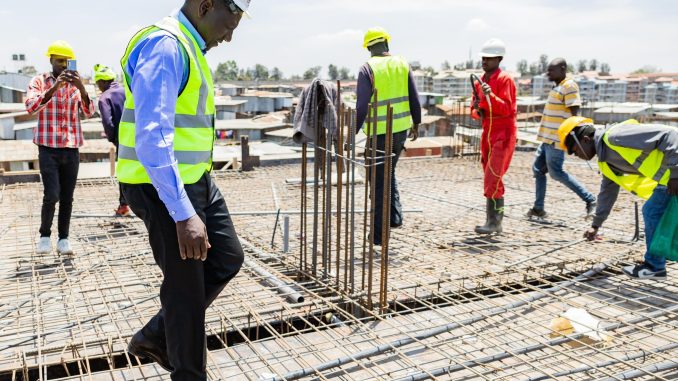
By Tobias Alando
In the chronicles of history, homesteads “Boma yangu” in Swahili stood as symbols of security, prosperity, and continuity for generations. In villages, building a home was not just a personal endeavour; it was a community affair that required everyone’s involvement – from the bricklayer to the carpenter. These communal efforts fed into the local economy, creating livelihoods, a sense of shared responsibility and more importantly dignified lives.
Today, Kenya’s modern-day version of “boma yangu” manifests in the Affordable Housing Initiative, a critical national agenda aimed at addressing the housing deficit and dignifying the lives of all Kenyans.
Yet, just like in the old days, the success of this project will depend on the contributions of every stakeholder. However, there is one key missing ingredient – a policy framework that ensures local manufacturers are at the forefront of this national initiative.
Affordable housing is not just a social welfare initiative; it is an economic game changer. Kenya faces a housing deficit of 2 million units, with demand increasing by 200,000 units each year, as reported by the Bottom-Up Economic Transformation Agenda (BETA). The government’s ambition to construct 250,000 homes annually through the Affordable Housing Plan aims at bridging this gap while stimulating the economy by promoting enterprise development in critical sectors like cement, steel, timber, and other construction materials. However, the absence of a robust local procurement framework is a significant barrier to fully realizing this vision for economic transformation especially one that proactively mandates contractors of affordable housing to source locally.
Just as village communities once thrived by utilizing local resources for homestead construction, today’s affordable housing projects can greatly benefit from local manufacturers. Unfortunately, while the Public Procurement and Asset Disposal Act mandates the preferential use of locally manufactured materials, this requirement remains largely unenforced. The absence of a stringent framework has allowed contractors to continue importing materials such as ceramic tiles and steel, even when local alternatives are available. This undermines the potential for local industries to grow and contribute to the economy.
To put this into perspective, despite Kenya’s capacity to produce 32 million square meters of ceramic tiles, data from UN Comtrade shows that imports in this sector tripled from $18 million in 2019 to $54 million in 2023. This growing reliance on imported goods represents a missed opportunity to strengthen local value chains and expand Kenya’s industrial base, particularly in sectors where domestic production capabilities are already well established.
One needs not look far for a working example of how affordable housing initiatives can benefit local industries. South Africa’s Preferential Procurement Policy Framework Act is a prime model. This policy compels contractors working on public projects to source materials locally, ensuring that the construction of affordable housing also strengthens the domestic economy. South Africa’s housing policy provides a valuable lesson for Kenya: when the government makes local procurement non-negotiable, the entire economy stands to gain.
Kenya can emulate this model by enforcing the Public Procurement and Asset Disposal Act and establishing mechanisms to track compliance. Requiring contractors to source materials such as roofing, tiles, paints, and fittings locally would stimulate domestic production, enhance competitiveness, and create jobs. Currently, Kenya’s construction materials sector directly employs over 100,000 people, with industries like steel alone supporting 25,000 jobs, according to data from the Kenya Association of Manufacturers. Strengthening local manufacturing through a structured procurement framework would not only boost employment but also drive sustainable economic growth.
The importance of supporting local manufacturers under the affordable housing project cannot be overstated. When local value chains are supported, the benefits extend beyond immediate job creation. They lead to economies of scale, reducing production costs, and enhancing the global competitiveness of Kenyan products. Local procurement also improves government revenue, as taxes generated from locally manufactured products directly benefit the nation.
However, without a digital platform to connect contractors with local suppliers, the procurement process remains fragmented. This is where innovation can play a crucial role. By creating a centralized online platform, the government can facilitate seamless interaction between suppliers and contractors, ensuring that local products are easily accessible and preferred. This move would mirror South Africa’s successful strategy and empower Kenyan manufacturers to compete on a level playing field.
Additionally, a revision of the Bill of Quantities (BQ) is needed to prioritize locally manufactured materials. For example, the BQ currently favours the use of APP membranes as roofing materials, discriminating against other roofing alternatives such as iron roofing sheets which are locally available in plenty. Adjusting these specifications would allow for more significant utilization of Kenyan-made products, ensuring that local manufacturers are not sidelined in the national housing agenda.
To ensure the success of the Affordable Housing Initiative, regular monitoring and stakeholder engagement must be a top priority. Bringing together manufacturers, contractors, juakali players, and government officials through frequent forums would track the implementation of local procurement policies and address emerging challenges. This collaboration would keep all parties aligned in promoting and strengthening Kenya’s local industries.
Looking at global examples, Brazil’s Minha Casa, Minha Vida (My House, My Life) program has effectively boosted its local construction industry by mandating the use of domestically produced materials such as cement and steel. This initiative, as highlighted in a report by UN Habitat titled Scaling-up Affordable Housing Supply in Brazil, not only facilitated the construction of millions of affordable homes but also created jobs and supported local suppliers. Similarly, Malaysia’s National Housing Policy has successfully implemented Import Substitution Industrialization strategies, promoting local industries like cement, steel, and wood in public housing projects. These examples illustrate the potential for Kenya to enhance its manufacturing sector by enforcing local sourcing in its Affordable Housing Initiative.
Kenya’s Affordable Housing Initiative is its modern-day ‘boma yangu’ – a project that, if implemented correctly, can do more than provide homes. It has the potential to create 300,000 additional jobs in manufacturing, triple government revenue from this sector, and ignite local innovation. Moreover, it aims to dignify the living standards of Kenyans, ensuring access to quality housing and improving overall quality of life. Beyond just providing homes, it holds the promise of transforming communities and enhancing livelihoods across the nation.
The time to act is now, and the solution lies within our borders. Let’s build Kenya, one locally sourced brick at a time.
The writer is the Ag. Chief Executive Officer of Kenya Association of Manufacturers and can be reached at ceo@kam.co.ke.
About The Author
Leave a Reply